The life of an offshore wind farm spans decades, and starts long before construction begins. Understanding each phase helps developers and stakeholders to reduce risk, stay compliant, and deliver cleaner energy to the grid.
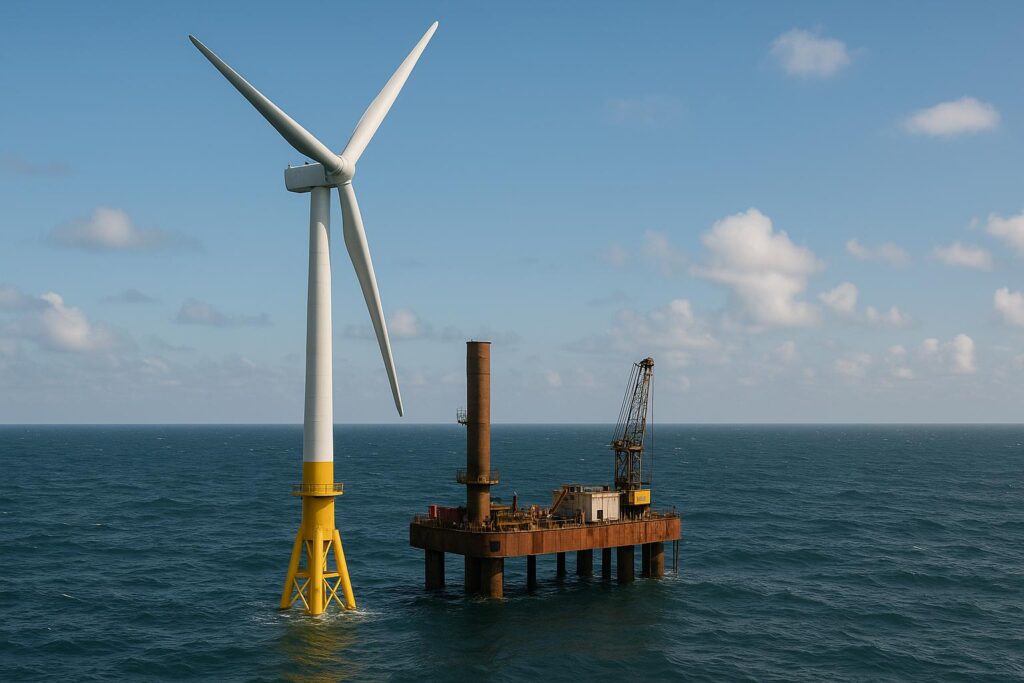
How long does a wind farm really last?
Most offshore wind farms are made to last for a 25-30 year operational lifespan, but that’s not exactly a fixed expiry date.
Turbine and wind farm lifespan depends on a number of factors: component wear, weather exposure, maintenance quality, and evolving regulation requirements. But robust planning, proactive O&M policies and practice, and mid-life upgrades can improve site development and farm viability.
Lifecycle planning isn’t just a paperwork exercise, it directly affects your ROI, insurance terms, and how offshore developments meet regulatory obligations.
Site assessment and project development
This first stage of the wind farm project life cycle can last years, and cost millions. Before turbine blades start spinning, developers need to assess their site’s potential; and this means balancing energy yield, environmental impact, seabed conditions, and stakeholder interests.
It’s not always an easy thing to master. The site assessment phase involves having to identify viable locations within applicable leasing zones (awarded by The Crown Estate), and carefully evaluating the following initial factors:
- Wind resource availability using wind speed measurements
- Wave climate and metocean conditions for safe weather windows and durability predictions
- Bathymetry and seabed geology to inform turbine foundation design
- Grid connection feasibility and proximity to ports
- Marine ecology and environmental risks requiring consultation with regulators
When each of these are considered balanced, then feasibility studies and environmental impact assessments (EIAs) are undertaken. This process can span up to three years and determines the technical, legal, and commercial viability of the offshore wind project.
In the meantime, you’ll need to engage local coastal or other potentially affected communities and get them on-side. Stakeholder engagement is also a legal requirement from this stage forward, especially under the UK’s Nationally Significant Infrastructure Projects (NSIP) regime.
Every offshore wind farm begins its life as data…
High-resolution environmental data is critical for early risk mitigation, and ongoing regulatory and social success. Get 500m-resolution insights, backed by 30 years’ hindcast data with the NeuWave platform – for 20x more accurate sea state reporting than industry standard.
Installation and commissioning of turbines
Once consent is secured (regulatory and social) and fabrication of the turbines themselves is underway, your attention shifts to the sea. Installation and commissioning of offshore turbines is a logistically intense moment in the wind farm life cycle.
Offshore turbines are designed and then built in parts. Foundations are laid at sea, and towers and blades assembled in a carefully staged sequence, often split between port-side prep and offshore lifts.
It’s also one of the most weather-sensitive phases of the life cycle. Timing is everything, and construction of offshore turbines can only happen during specific weather windows.
Marine operations are constrained by wave height, wind speed, tidal patterns, and visibility conditions. The cost to operations can spiral into the millions, with delays caused by both poor weather and missed safe weather windows.
By using intelligent tools and reliable data, developers are able to:
- Forecast accurately and maximise safe operating windows
- Choose the right vessel for each operation
- Schedule cable laying and installations to reduce idle time
- Predict and plan around seasonal bottlenecks
Commissioning involves rigorous safety and control system checks and tests, and can begin once turbines are in place and grid connections are established. Each turbine should be brought online individually, and full commissioning of a wind farm can take weeks to months (depending on scale and real-time conditions).
Building solid turbines hinges on more than just modern kit…
It relies on how well the sea is understood by developers, stakeholders, and regulators. By combining deep learning and high-resolution modelling, NeuWave helps project teams forecast more than just the weather. Mitigate delays, predict costs, and spark opportunity.
Operations, maintenance, and servicing
Turbines rotating doesn’t mean the work stops. This is really just the start (again). Offshore wind farms are built to last decades, and they demand constant attention to stay not only productive and profitable, but also safe and operational.
Operations and maintenance (O&M) costs typically make up to 20-25% of a wind farm’s lifetime budget. It sounds like a lot, but this includes routine inspections, replacing worn components, addressing unplanned repairs, and any remote or physical monitoring of performance and energy yields.
There’s a small army of tools, platforms, and devices – not to mention specially-trained humans – used to make this happen. Developers often rely on real-time SCADA systems, drones, autonomous vessels, and O&M teams to keep everything running smoothly.
When it comes to maintenance, accessing turbines is dependent on safe wave heights, wind speeds, and local weather conditions. Keeping operations resilient and efficient requires access to:
- Long-term hindcast data to help understand seasonal weather trends
- High-resolution forecasts for route planning and vessel dispatch
- Tools to simulate downtime risk and optimise scheduling and planning
- Port-level visibility to coordinate access with local infrastructure limits
Even minor repairs can face weeks of delay if access vessels can’t get to them, with missed or inaccurately reported maintenance windows meaning many crews are either inefficient or unsafe.
It’s a logistical nightmare and offshore conditions don’t make it any easier.
Many developers rely on fragmented or incomplete data…
This is where NeuWave makes the difference. Our precision wave models are calibrated with 30 years of hindcast data and accurate to within 15cm. Helping offshore teams make safer, smarter, and more dynamic decisions.
Decommissioning an offshore wind farm
Decommissioning is the final phase in wind farm development; but equally as complex as any of the others.
By the time a wind farm reaches the end of its lifespan, it’s usually operating under different legislation, newer safety standards, and (often) a more crowded marine environment than when it was planned and built.
Developers are legally required to remove all infrastructure that poses environmental or navigational risks. This includes foundations, cables, and turbines – all of which demands the same level of precision, planning, and weather-sensitivity as installation and operations.
It also carries new challenges: unknown corrosion levels, equipment fatigue or failure, and tighter regulations around seabed restoration and recycling. It’s slow, expensive work. And while many developers hope to repower rather than dismantle, early planning for decommissioning is non-negotiable.
Offshore wind might be a long game, but nothing lasts forever.
Repowering vs. decommissioning
As the first generation of offshore wind farms is nearing its end-of-lifecycle, the question of dismantling versus repowering becomes highly relevant.
Repowering (replacing older turbines with newer, more efficient ones) is becoming an attractive alternative to full decommissioning, offering environmental benefits, potential cost savings, and a chance to increase capacity within the same footprint.
But it’s not always that simple. Repowering still requires updated EIAs, grid connection assessments, compliant infrastructure, and sometimes renegotiated leases.
Maintain data continuity from the start…
One of the biggest challenges of repowering? Maintaining long-term data continuity. NeuWave supports developers with the long-range, site-specific data needed to evaluate repowering feasibility and future-proof asset planning.
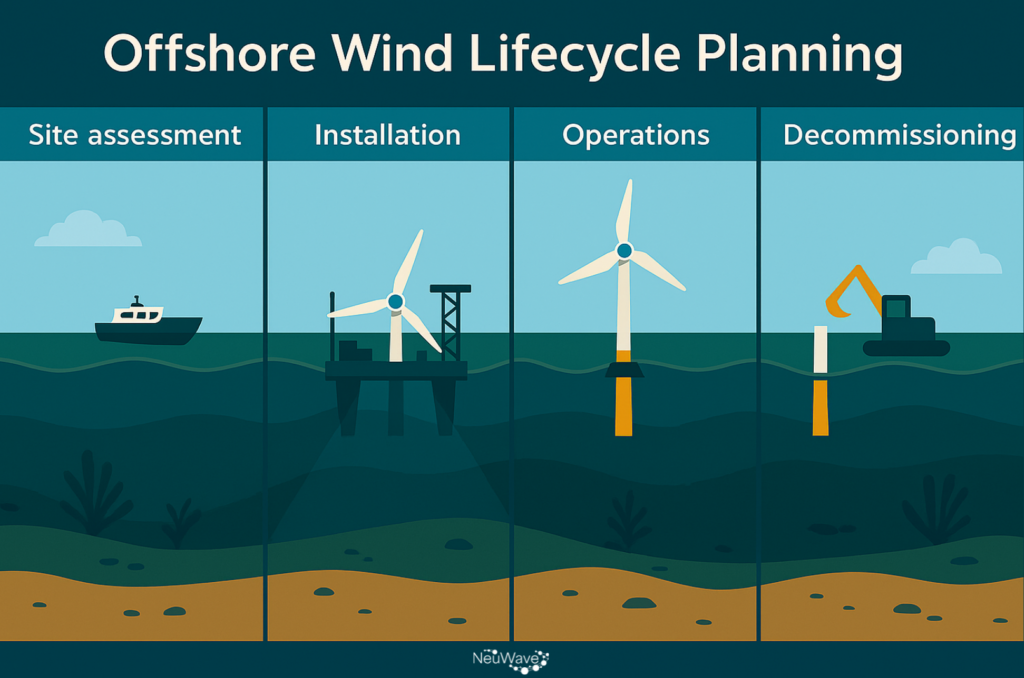
What happens to wind farm waste materials?
Materials from wind farms don’t just vanish, and decommissioning leaves behind thousands of tonnes of steel, copper, concrete, and other composite materials. While metals like steel and copper are widely recycled, turbine blade materials remain a challenge for the industry.
Some are now being repurposed into construction materials, bridges, or even playgrounds. Others end up in landfill – something the industry is under increasing pressure to avoid. Foundations and subsea cables can often be removed and reused or recycled, depending on condition and legislation.
As the first wave of offshore wind farms reaches retirement age, circular economy strategies are urgently needed. Designing for disassembly, improving material traceability, and tracking degradation over time, will be key to managing the sector’s end-of-life impact.
Powering precision from day one to decommission
The NeuWave platform supports developers with high-resolution, verifiable marine data, enhancing planning, forecasting and compliance. Drive smarter decisions, reduce downtime, and build truly resilient, robust wind farms that can service the renewable energy needs of the future.